Pre-Shipment Inspection (PSI) for Quality Control before Shipment
Ensure your products meet your requirements before the production run is finished and your products are packed for shipment.
QIMA’s pre-shipment inspection is an intensive on-location examination conducted when 80% of your production order is complete. Our service helps you check if your products meet all required specifications, allowing you to take corrective actions before your production order is finalized.
Learn more about:
What is a Pre-Shipment Inspection (PSI)?
Why Do You Need a Pre-Shipment Inspection?
What Checks are Carried Out?
QIMA’s Pre-Shipment Inspection (PSI)
What Happens after a PSI is Completed?
QIMA Expertise
QIMA Benefits
What is a Pre-Shipment Inspection (PSI)?
A pre-shipment inspection ensures your products meet your quality specifications before they are shipped. When at least 80% of your order is complete, an inspector visits the factory and uses industry-standard processes to comprehensively review and test your product. You’re provided with a full report, accessible through our online platform.
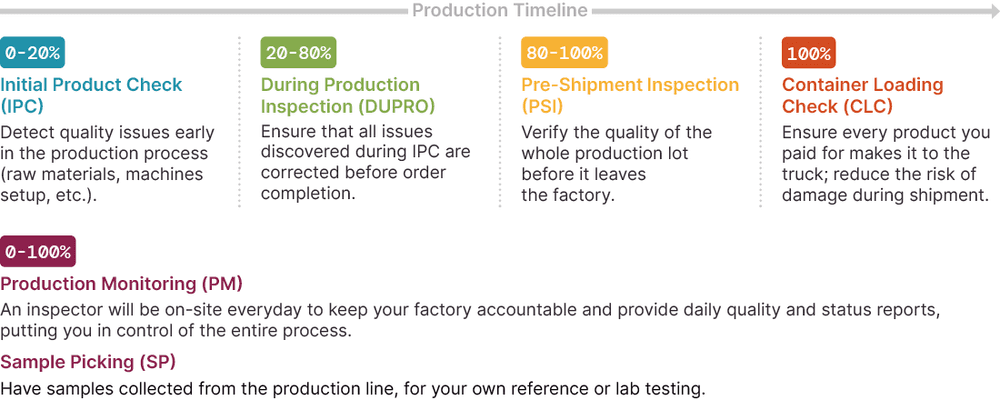
Need more information?
By contacting QIMA you agree to our privacy policy and terms and conditions.
Why Do You Need a Pre-Shipment Inspection?
Pre-shipment inspections conducted by a neutral third party are industry standard for ensuring your product meets your quality specifications. Defective or subpar products could lead to customer complaints, returns, lost sales, and damage to your company’s reputation.
With our pre-dispatch inspection, you get peace of mind that your order has been fulfilled correctly before shipping.
There are several reasons to use our PSI:
Ensure that your supplier has met all agreed-upon specifications: This helps to prevent misunderstandings and ensures that the products delivered are exactly what was requested.
Verify quality standards with off-the-shelf or custom checklists: Custom checklists can be tailored to your specific needs based on your unique criteria.
Check production progress: Identify any delays before they impact your delivery schedule.
Take corrective action before it’s too late: Implement solutions promptly, minimize disruptions to production and shipping.
Prevent returns and protect your brand’s image: By ensuring quality before shipment, you reduce the likelihood of customer complaints and returns.
Verify final product quality when you can’t access the factory yourself: With our PSI, you can maintain quality assurance without being physically present.
It’s not a good idea to rely on your factory to tell you that the products meet all specifications. Our PSI experts will provide an unbiased, thorough assessment of your production order.
What Checks are Carried Out?
The QIMA inspector will first randomly select a sample of products for inspection, following the ANSI/ASQ Z1.4-2008 sampling standard.
After the sample has been selected, the inspections are tailored to fit client needs and specific products.
We provide a variety of pre-designed inspection checklists suitable for different products, which you can use "as-is." You also have the option to modify these checklists by adding particular checks, or you can develop a completely new checklist that caters to your specific requirements.
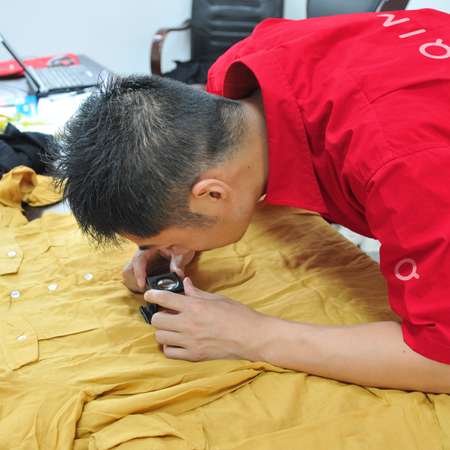
QIMA’s Pre-Shipment Inspection (PSI)
QIMA conducts a comprehensive PSI that involves a series of meticulous checks, typically including the following:
Product specifications checks:
Quantities of semi-finished, finished, and packed products
Product colors, style, construction
Artwork including spelling, fonts, dimensions, positioning, design
Main labels, care labels, size labels, product tags
Other product-specific checks and tests
Functional testing
Material composition check
Other relevant tests
Workmanship defects checks
Imperfections check
Assembly process check
Consistency across all products
Product dimensions check
Length, width, height
Unit weight check
Packing and packaging checks:
Inner and outer unit packing
Export carton dimensions and weights
Shipping marks on cartons
What Happens after a PSI is Completed?
Once a pre-shipment inspection is completed, you’ll receive a detailed inspection report the same day. You’ll be able to easily access the report through your online QIMA account. The report details the inspection findings, includes photos of any defects, and gives an overall pass/fail assessment.
QIMA Expertise
QIMA provides independent quality control designed to protect your business interests. Our highly trained and experienced inspectors are product experts who undergo regular training in their field of specialization. They can be on-site at your factory within 48 hours of booking and provide the report on the same day as the inspection.
Our inspections cover a full range of consumer products, including but not limited to apparel, footwear, toys, electronics, and furniture.
Create an account and book a PSI
Take your quality management online
QIMA offers an intelligent online platform to help you seamlessly manage your quality control and global supply network.
You can easily book, cancel or reschedule inspections, make payments or download your inspection reports with a few clicks. We also provide a customizable dashboard with all of your quality control data, so you can identify trends and make informed decisions in real-time.
QIMA Benefits
Independent quality control performed by product experts to protect your business interests.
Global coverage across 100 countries in Asia, Africa, Europe, North and South America.
Speed and flexibility with an inspector onsite within 48 hours; modify or cancel up to the day before inspection.
Same-day inspection reports tailored for your product.
Online program management to book inspections, make payments, and download detailed reports.
Custom quality dashboard to identify trends and make informed decisions in real time.
Ranked #1 in the industry for customer satisfaction based on independent NPS measurement.