The Australian Children’s Toy Market
The Australian toy market is a $5 billion industry with the majority of toys being manufactured in China. Like many countries, toy safety regulations in Australia require manufacturers to perform testing on their products before they are legally allowed to sell into the market. Australia’s toy market is regulated in a similar way to the EU and US markets - with strict standards that dictate the minimum requirements to sell within the country. If you are a manufacturer, importer or retailer selling in the EU or US, you may already be in compliance with Australia’s standards. If not, the barriers to entry may be less challenging than you think.
Here, we will explain Australia's toy safety standards to give you an idea of how close you might already be to selling your products in the Australian market.
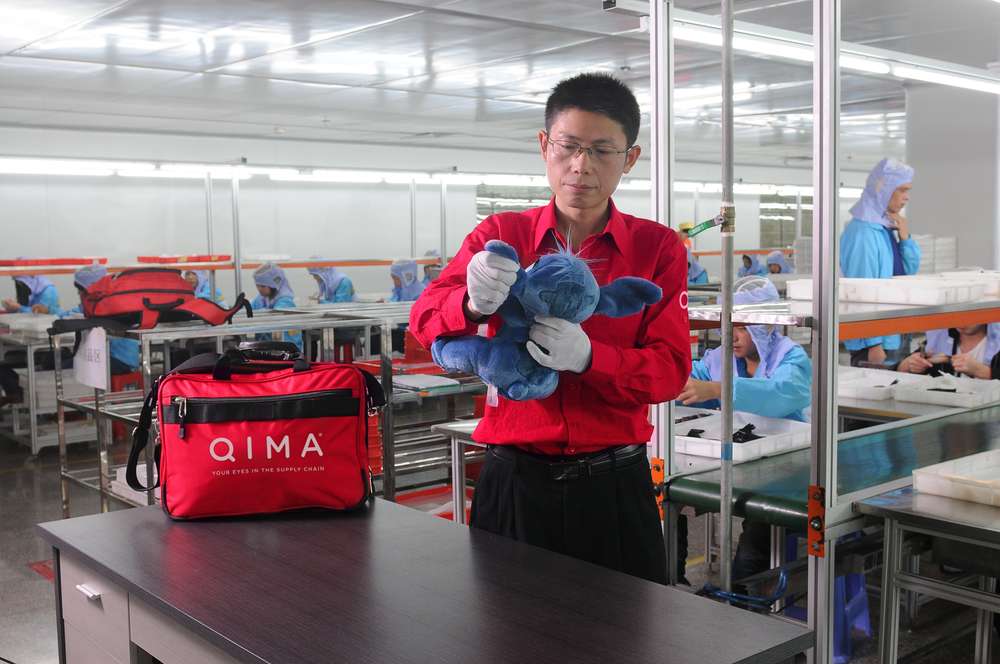
Need more information?
By contacting QIMA you agree to our privacy policy and terms and conditions.
Australia’s Five Mandatory Toy Safety Standards
Mandatory toy compliance is divided into five categories, and the majority of Australia’s regulations are harmonized with the Australian/New Zealand standard AS/NZS ISO 8124, International standard ISO 8124, European Standard EN 71 or American Standard ASTM F963. The following five mandatory Australian toy safety standards are required before your product can be legally marketed in Australia.
1: Toys For Children Up To and Including 36 Months of Age (Safety Standard 2023)
The purpose of this standard is to minimize the risk of small parts detaching from toys during use or after normal wear and tear, thereby reducing the potential for choking, suffocation, or harm for toys intended for children up to 36 months of age.
The mandatory standard allows compliance with certain sections of one of the following:
Australian standard AS/NZS ISO 8124.1:2023 Safety of toys – Part 1: Safety aspects related to mechanical and physical properties
International (ISO) standard ISO 8124‑1:2022 Safety of toys – Part 1: Safety aspects related to mechanical and physical properties
European (EN) standard EN 71‑1:2014 + A1:2018: Safety of toys – Part 1: Mechanical and physical properties
American (ASTM) standard ASTM F963‑17 Standard Consumer Safety Specification for Toy Safety.
Testing requirements cover, but are not limited to:
Small parts – For children up to and including 36 months
Partial test of shape, size, and strength of certain toys
Mouth-actuated toys
Examples of toys held to this standard include: rattles, teethers, toy cars, dolls, bath toys, push and pull toys, games and puzzles; as well as "toys for attaching to cots, playpens, prams and strollers." A more comprehensive list can be found on the ACCC's product safety website.
The mandatory standard also mandates that all toys intended for children up to 36 months of age, and equipped with any type of battery, must have the battery compartment securely sealed in a manner that requires the use of a tool for access.
2: Children's Projectile Toys (Consumer Goods (Projectile Toys) Safety Standard 2020)
This standard addresses potential eye injuries, choking hazards and flesh wounds.
A projectile toy should comply with the relevant sections for projectile toys in one of the following four standards:
AS/NZS 8124.1:2019 - Safety of Toys - Part 1: Safety Aspects Related to Mechanical and Physical Properties (including amendments 1 and 2)
EN 71-1:2014+A1:2018 Safety of Toys - Part 1: Mechanical and Physical Properties
ISO 8124.1:2018 Safety of Toys - Part 1: Safety Aspects Related to Mechanical and Physical Properties (including amendments 1 and 2)
ASTM F963-17 Standard Consumer Safety Application for Toy Safety.
These standards address the following aspects of the projectile toy:
The maximum force at which projectiles can be launched
Protective measures for projectiles that present a skin puncture hazard
The size of projectiles
Features to prevent improvised projectiles from being launched in a hazardous manner.
Moreover, these standards also contain labelling requirement for projectile toys that are capable of launching a projectile more than 300 millimeters or with a kinetic energy greater than 0.08J.
Examples include toy guns, slingshots, bow and arrow sets, and dart guns. Suction cup projectile tips can pose potential choking hazards if the small suction cup breaks off of the projectile shaft through repeated bending and pulling.
3: Children's Toys Containing Magnets (Consumer Goods (Toys Containing Magnets) Safety Standard 2020)
The ingestion of magnets has the potential to cause choking and infection. When swallowed in pairs, they can cause severe intestinal blockage and perforation, which can be fatal. The standards and testing requirements below are designed to reduce the risk of children ever swallowing the toy in the first place.
Toys containing magnets must comply with the relevant sections for magnets in one of the following four standards:
AS/NZS 8124.1:2019 - Safety of Toys - Part 1: Safety Aspects Related to Mechanical and Physical Properties
EN 71-1:2014+A1:2018 Safety of Toys - Part 1: Mechanical and Physical Properties
ISO 8124.1:2018 Safety of Toys - Part 1: Safety Aspects Related to Mechanical and Physical Properties
ASTM F963-17 Standard Consumer Safety Application for Toy Safety
These standards include several testing requirements.
4: Aquatic Toys (Consumer Goods (Aquatic Toys) Safety Standard 2020)
This standard is directed at aquatic toys (specifically, those for use in play in shallow water designed to bear the mass of children under 14 years old). The main focus of this standard is on prominent warning labels. Australian safety standards demand that aquatic toy manufacturers make it clear that their product is not a safety device, and that children should never be left unaccompanied while using these products.
Aquatic toys must comply with the relevant sections for one of the following two standards:
Australian/New Zealand Standard AS/NZS ISO 8124.1:2019 Safety of toys Part 1: Safety aspects related to mechanical and physical properties
International Standard ISO 8124-1:2018 Safety of toys - Part 1: Safety aspects related to mechanical and physical properties.
For example, the standard requires that the air inlets of inflatable aquatic toys must be non-return valves with stoppers permanently attached.
Moreover, aquatic toys must carry a statement that clearly indicates that the toy is not a life-saving device, followed by a warning that the toy should only be used in shallow water under adult supervision. There must not be advertising content that states or implies a child will be safe if left unsupervised.
5: Lead and Other Elements in Children's Toys
Because the nature of play involves sustained contact with toys, including contact with the skin and mouth, this standard addresses the hazards of heavy metal ingestion and absorption through the skin. Exposure to heavy metals can cause both immediate illness and long-term developmental disorders. This standard derives from AS/NZS ISO 8124.3 'Migration of Certain Elements' and AS 8124.7 'Safety of Finger Paints'.
Testing requirements cover:
Maximum acceptable element migration from toy materials (AS/NZS ISO 8124.3.4)
Limits for migration of certain elements from finger paints (AS 8124.7.4.4)
Note: For finger paints, Australia enforces a lower and stricter migration limit compared to ISO 8124.7.
Toy safety regulations in Australia are determined and enforced by the Australian Competition and Consumer Commission (ACCC), which oversees products from motorized vehicles to food products. They maintain a regularly updated website with features including product safety laws and recall notices. Conveniently, the ACCC categorizes their standards by product, so you can click your product category to access the associated regulatory requirements.
Accredited Lab Testing for Safety Assurance
The ACCC understands the importance of accredited lab testing and factory inspection as the best measure against introducing unsafe toy products to the Australian market. Product testing by an accredited lab service versed in all national and international standards will ensure that your toy product is compliant.
In addition, our labs evaluate your product for:
Categorical bans of your product
Functional or aesthetic defects
Accuracy of claims made about the product
QIMA offers fully accredited lab testing expertise so you are never in the dark about the quality and compliance of your toy and recreational equipment. We have deep factory inspection experience in Chinese factories, where the majority of toy products are manufactured (68% of toys sold in Australia are imported from China).
Easily Schedule Your Toy Tests Online
Our online platform and mobile application make it easy for you to schedule testing, and receive your results at any time. Book new tests, view pending orders, and access results from your mobile device. Our online platform provides valuable supply chain insights, including a summary of your QC activity, all of your supplier’s quality stats, industry benchmarking data, and more.
Get Started: Login or Create Your Account
OR: Ask A Question (We respond within 24hrs)
The QIMA Benefits
Global coverage in over 100 countries in Asia, Africa, Europe, North and South America.
Flexibility with fully customizable programs and reports to save time and cost.
Risk-based approach with analytical data to help you proactively identify and prevent quality and safety issues in your supply chain.
Fully certified and accredited to all major inspection, audit and testing schemes.Custom dashboard to identify trends and make informed decisions in real-time.
Personalized service with dedicated account manager and 24 hour customer support.
QIMA Benefits
Global coverage in over 100 countries in Asia, Africa, Europe, North and South America.
Flexibility with fully customizable programs and reports to save time and cost.
Risk-based approach with analytical data to help you proactively identify and prevent quality and safety issues in your supply chain.
Fully certified and accredited to all major inspection, audit, and testing schemes.
Custom dashboard to identify trends and make informed decisions in real time.
Personalized service with dedicated account manager and 24-hour customer support.
Ranked #1 in the industry for customer satisfaction based on independent NPS measurement.
More Resources
test - Download a toy testing sample report for insight into the toy testing process.
Pet Toy Testing - Read about our pet toy testing services and regional requirements.
Toy Safety Checklists - View our guide on how to establish your toy safety checklist.